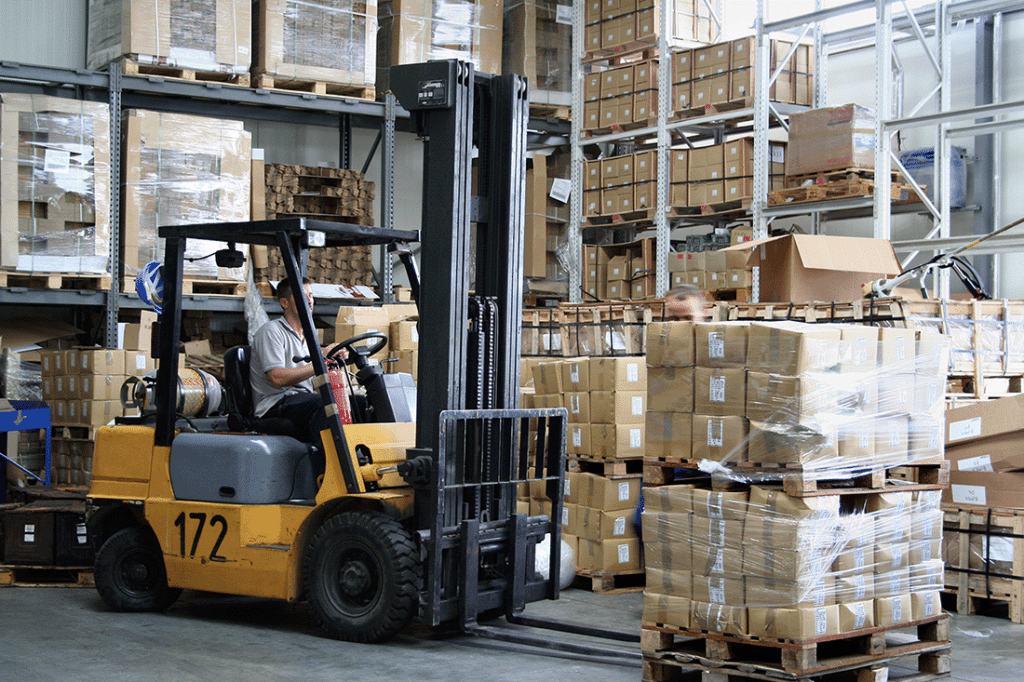
Companies frequently approach us to implement RTLS systems for tracking their forklifts, and at times, that suffices. However, we often identify a greater potential to monitor all critical company assets—not just forklifts. Once a WISER ATLAS UWB RTLS forklift tracking system is in place, the infrastructure is established, prompting us to question: why not track forklifts, what they are moving, and anything else that’s job-critical?
In the dynamic landscape of modern manufacturing, staying ahead of the competition demands efficient operations, streamlined workflows, and the ability to make informed decisions. Enter Real-Time Location Systems (RTLS), a technology that has the potential to revolutionize the way you manage your manufacturing facility. Not only does it enable precise monitoring of forklifts, but it also opens a world of possibilities by allowing you to track the assets they transport and other things that get moved, creating a comprehensive tracking solution that can redefine your facility’s logistics.
A Holistic Approach to Manufacturing Operations
By extending the capabilities of RTLS beyond forklifts and encompassing the various assets being transported, you unlock a treasure trove of insights into your facility’s operations. This all-encompassing approach offers a range of advantages, including enhanced visibility, improved asset utilization, asset protection, loss prevention, and data-driven decision-making.
Enhanced Visibility
Expanding the scope of tracking to include the items carried by forklifts, pallet jacks, lift trucks, buggies, tugs, conveyors or any other transporter provides real-time visibility into their whereabouts, movement history, and current trajectories across your manufacturing facility. This real-time vantage point allows for seamless monitoring of asset progress, ensuring that items adhere to their designated pathways and reach their destinations on time. It allows for exceptions and priority handling—such as time-sensitive rush orders or product nearing expiration dates—and can improve quality control monitoring. This increased transparency plays a pivotal role in reducing shrink, optimizing workflows, streamlining operational processes, and minimizing delays or bottlenecks in manufacturing, operations, and inventory management processes.
Improved Asset Utilization and Production Planning
Full-scale tracking enables efficient monitoring of asset utilization. Analyzing data on asset movement patterns allows you to identify underutilized resources and instances of prolonged idleness. This data-driven approach empowers you to make informed decisions to optimize resource allocation, production planning, enhance utilization, and reduce downtime.
Asset Protection and Loss Prevention
The inclusion of asset tracking alongside forklift monitoring autonomously enhances security measures within your facility. In cases of unauthorized movement or potential theft, the RTLS system can swiftly identify the last known location of the asset, aiding in its recovery. Moreover, continuous monitoring with alerts for unauthorized activity acts as a deterrent against loss, reducing the likelihood of valuable items going missing.
Data-Driven Optimization
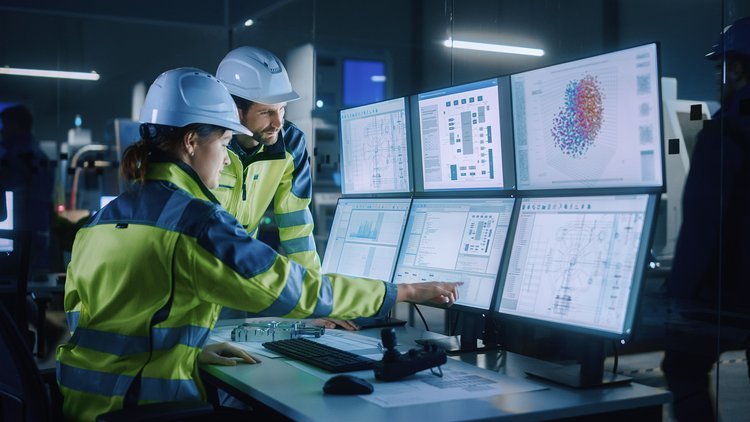
Integrating asset tracking into your RTLS system generates a wealth of data for informed decision-making. Analyzing data from both systems helps identify patterns, trends, and operational inefficiencies. This data-driven approach enables you to enhance operational performance, allocate resources effectively, and identify areas for optimization.
Unleash Efficiency and Productivity
Consider the ripple effect of unplanned downtime – it not only consumes time searching for lost items but also hinders revenue-generating activities. For instance, an average automotive manufacturer loses $22,000 per minute during production stoppages, as revealed by insights from Forbes, Inc. Overall, unplanned downtime costs industrial manufacturers as much as $50 billion a year. By contrast, a meticulously tracked workflow optimizes workforce utilization and enhances productivity, producing cost savings that enhance the bottom line. Imagine optimized travel paths, judicious resource allocation, and efficient processes – where wasteful redundancies and time spent searching for lost items are eliminated.
Incorporating a UWB RTLS solution within your facility establishes a comprehensive framework encompassing forklifts, equipment facilitating asset transport, and the full spectrum of assets requiring tracking across the facility. This strategy not only amplifies efficiency and productivity, but also yields priceless insights for finely tuned operational optimization. Leverage the potential of UWB RTLS and let your asset tracking solution lead your digital transformation journey towards more intelligent Industry 4.0 operational automation.