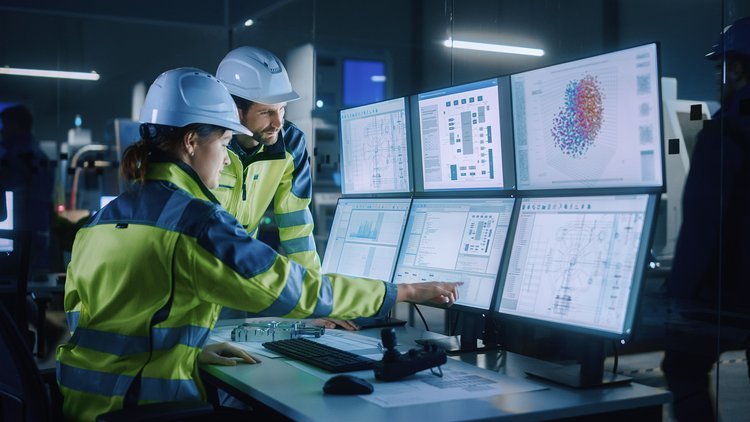
RTLS Data technology has advanced significantly in recent years. How manufacturers achieve precise data with UWB RTLS technology is crucial to their success in making data-driven decisions to optimize processes and enhance value in their challenging industrial environments.
Real-time tracking of assets, inventory, and personnel allows for dynamic decision-making, streamlined workflows, and reduced downtime. As smart factories continue to evolve, the strategic implementation of UWB RTLS data will be a cornerstone of their success, enabling a new era of industrial innovation and competitiveness.The following information draws from WISER’s experience of testing and validating the use of RTLS technology in heavy industrial manufacturing environments using our mesh network ultra-wideband (UWB) RTLS solution.
Here are the main topics that will be discussed:
Chapter 1: The promise and challenge of location data in Industry 4.0
Chapter 3: What are the benefits of RTLS?
Chapter 4: What are longer term benefits of RTLS?
Chapter 5: Evaluating an RTLS solution: Which RTLS system is right for you?
Key challenges to manufacturers today
The advent of Industry 4.0 and the adoption of digital transformation technologies is proceeding rapidly and manufacturers are grappling with rising costs of labor, inventory management, and worker shortages. Automation provided by software, hardware or robotics applications are ubiquitous and choices proliferate. But not all solutions are created equal when it comes to boosting industrial productivity. All-in-one solutions, may, in the end, have only marginal benefits given costly disruptions in operations and the high cost of training employees on new processes and platforms.
Among the low-hanging fruit for Factory of the Future innovations, real-time location technologies may be both the most cost-effective and least disruptive, and most appreciated by employees – allowing for near-immediate ROI with an order-of-magnitude boost in productivity and output.
Chapter 1: The Promise and Challenge of Location Data in Industry 4.0
Industry 4.0 is the promise that by marrying automation and big data with what’s happening in the real world, companies can substantially improve their performance and competitiveness. To fully capture the benefits of Industry 4.0’s opportunities, companies will require an array of sensor and analytical solutions.
However, for the analytics to be useful, the quality of the data will be critical. Consumers have benefited from high quality outdoor data generated by GPS. With your phone, you can find where you want to go, how to get there, and even how to avoid a temporary roadblock on the way.
Increasingly, manufacturers are demanding location type data inside the factory and warehouse at a more granular level, perhaps to the nearest foot or even down to inches, to track thier manufacturing processes. This would give the manufacturer real-time insight into where all the critical components are at any point in time and where, when, and how bottlenecks occur. Real-Time Location Systems (RTLS) are now delivering on that promise and can scale to monitor the location of thousands of objects in real-time.
According to Deloitte’s 2024 Manufacturing Outlook, “Manufacturers with higher digital maturity before COVID-19 had an advantage to some extent with greater resilience, as did those that accelerated digitalization during the crisis.” RTLS is often the first of many digital strategies manufacturers consider for all of these reasons. In addition, many manufacturers expect that weather events, fires, and similar problems may increase with global warming and companies need to have flexible strategies to prepare and respond to unexpected changes.
Chapter 2: What is RTLS?
The term RTLS typically refers to localized positioning systems, as opposed to global positioning systems such as GPS. While time and location are the obvious common aspects of both, identification is an additional important feature of RTLS, even in cases where identifying information is safeguarded.
In essence, RTLS shows the what, where, and when within a defined locale, quantifying these factors in a way decision-makers can understand. For instance, RTLS could be used to show which workorder (what) crossed a given production area in a manufacturing facility (where) at a specific time (when). Another example: RTLS can visualize which shippable container (what) was loaded onto a specific truck (where) at a given point during the workday (when).
Because RTLS describes a wide array of location intelligence solutions, it’s helpful to disambiguate. For instance, the term RTLS generally encapsulates systems providing proximity-based data or actual coordinates. It’s also commonly (and erroneously) used for systems that identify devices at set choke points, providing only temporary location at a point of scan.
Most RTLS solutions include a series of antennas positioned around the space to be monitored which capture location information from tags attached to assets or personnel as they move in real time. These systems generate the tags’ location data in real-time and often offer movement history readouts as well.
Chapter 3: What are the benefits of RTLS?
The knowledge of asset location is extremely valuable even before any data analytics are performed.
Some of the benefits include:
- Better inventory management – finding lost inventory, and recovering the cost it would have taken to replace it, recovering lost work hours looking for it, or eliminating unplanned downtime for routine inventory checks. All create value in a factory setting, by avoiding unnecessary replacement by saving plant workers time and in turn increasing efficiency and productivity to reduce operational costs per item manufactured, and ultimately increase the bottomline.
- Greater efficiencies in manufacturing processes, including work in progress tracking, finding lost or repaired machinery, and identifying bottlenecks.
- Increased worker safety
- New and improved business intelligence for continuous improvements
Inventory Management
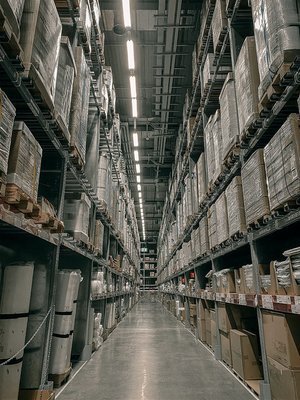
Being able to find raw materials and parts, tools, and inventory immediately is incredibly important for a manufacturer to operate efficiently. Because factories are often messy places with moving parts and changing shifts of people, items get misplaced.
This problem will only grow as companies move away from just in time manufacturing to storing more inventory on site. The New York Times explains, “Cheap and reliable shipping may no longer be taken as a given, forcing manufacturers to move production closer to customers. After decades of reliance on lean warehouses and online systems that monitor inventory and summon goods as needed — a boon to shareholders — manufacturers may revert to a more prudent focus on extra capacity.” As such, digital tools can help factories manage these larger inventories.
Dr. Richard Soley, executive director for the Industrial Internet Consortium (IIC) described a “‘client [who] found that its workers spent 47 percent of their time just looking for the right tools.’ [He continued to explain…] with an IIoT solution, the worker could be told that the tool they needed was 10 meters behind them and to the left.” WIRED magazine
When these inventory cases occur in a manufacturing facility, a more precise solution that can handle highly reflective environments is needed. In such cases, UWB RTLS is normally the best solution. UWB is a short-range, wireless communication protocol that – like Bluetooth or Wi-Fi – uses radio waves. But it differs substantially in that it operates at a very high frequency and allows for more precise location data that other technologies. UWB is explained further in Chapter 5, sub section on “What is your Operating Environment? RTLS in Heavy Metal, Reflective Environments.”
Greater Efficiencies in Manufacturing Processes (Produced by real time locating and tracking)
RTLS can be valuable to improving the productivity of many types of manufacturing processes including wheel manufacturing, cellular manufacturing, batch manufacturing, and WIP methods where each order moves through a set of steps or stations that vary from order to order. WIP often requires holding partially completed product for a period of time until a station or part is available for the next step. With supply chains continuing to suffer delays and blockages, aspects of WIP manufacturing are becoming the norm for many manufacturers who aren’t traditionally associated with these methods. Recently, even auto manufacturers are having to store partially completed automobiles while waiting for a required chip to arrive. When the part arrives they must find the specific vehicle it was meant for, and seamlessly insert it back into production.
For more detail on RTLS systems in WIP manufacturing visit, “A critical look at how manufacturing work in progress (WIP) can be improved and lean waste reduced or eliminated to increase your bottom line.”
Quickly Finding Lost or Repaired Machinery
Most modern factories already have several automated or robotic machines that require regular and at times complex maintenance. One promise of smart factories is using sensors to identify machines that need repair before they break down to allow the factory the chance to swap out machines or parts at more convenient times. However, when making swaps, it’s not always that easy to find the missing machine. Some parts, such as robotic heads, which are critical at times, get lost in busy factories. A UWB RTLS system allows workers to easily find any part and, based on location, identify whether the machine is repaired or in use. This can again save workers time hunting down machines, smooth out the repair and maintenance cycle, and potentially extend the life of valuable machinery. Wi-Fi and Bluetooth RTLS solutions have greater difficulty providing required accuracy because of problems dealing with reflection and line-of-sight problems that occur around large machines made of metal in close proximity.
Finding Bottlenecks
Most RTLS solutions generate historical data, where the user can see critical assets move throughout the day. With a simple time-and-motion analysis, a plant manager can use that data to look for bottlenecks in the manufacturing process, storage and retrieval of supplies, or other areas. They can do short-term studies on employee movement for safety and efficiency. Plant managers can rearrange supply storage areas of the production floor to make it more efficient and safer based on actual movement data. Having quantitative data as a basis of current and future decision-making can yield huge, long-term improvements in efficiency.
How to find and solve bottlenecks in manufacturing.
Adding Business Intelligence
Another area where RTLS systems can provide operational benefits is by adding business logic intelligence and alerts to the system. One example is the creation of geofencing capabilities where RTLS can identify zones that adhere to different rules. One WISER customer is a major manufacturer of large construction equipment that is often customized. When a piece of equipment completes a first station and moves to the next zone, the manufacturer wants to bring the correct tools and supplies for the next piece of construction equipment traveling to that first station. In this case, the RTLS solution sends an alert to the supply area whenever a piece of equipment moved to another zone. The supplier then knows to prepare and deliver the correct tools and supplies to the first zone. With the increasing use of robotics, the message could be sent to a robot to perform the task, as well.
Again, because this facility handles large pieces of metal construction equipment which frequently block line-of-sight, a UWB solution that is not compromised by tracking errors caused by heavy metal signal reflections is optimal for this environment.
Increased Worker Safety
Managers can be provided with alerts and geofencing options that can help increase employee safety. If an employee gets too close to a crane, repair area, or large piece of dangerous equipment, they and the equipment operator can be alerted. Managers can also be alerted if an employee has worked too long in an area with significant amounts of lifting, were subjected to loud noise for a prolonged period, or have performed repetitive movements or worked for too long on the same piece of equipment. They can then inform the worker to take a break to avoid work-related injuries.
Another solution to improve efficiency is pairing sensors to the location system itself. For example, some RTLS tags also provide climate, acoustic, and other data as well. At times, these sensors can be embedded into the tags or paired with alerts through the RTLS software. Manufacturers can identify areas that may be overheating, too cold, too loud, or have hazards for optimal manufacturing. They can look for malfunctions on moving items such as forklifts, robots, drones, etc. For any asset or piece of machinery that moves through a facility, an RTLS system paired with sensors and alerts can improve the quality of data delivered to users.
Chapter 4: What are Longer-Term Benefits of RTLS?
RTLS clearly offers a multitude of benefits for the manufacturer today. Looking at the future, companies are on the cusp of a real digital transformation. Good location information will be a cornerstone for the success of those companies that embrace Industry 4.0. As processes become ever more automated, robotics becomes more central to the manufacturing process, and AI becomes a real part of manufacturing decision making, accurate, reliable location data will be critical, both in and of itself, as well as to the successful roll-out of these and other technologies.
For process automation to work, users, robots, and decision-making software all need good visibility into where orders are located, where inventory is, or where employees are working. If that information is inaccurate or delayed, these automation systems cannot properly assess the situation, cannot send the required alerts to personnel or robots, or summon the necessary worker for a given task.
With the increased use of mobile and autonomous robots in manufacturing, delivering accurate information to the robots on potential obstacles in their location, and how to avoid them, becomes increasingly important. Moving some of the robot’s location intelligence to the facility wide mesh-networked RTLS can reduce the cost of each individual robot as well.
UWB RTLS will best meet the accuracy requirements to support robot movement, especially when robots move behind an object and line-of-sight is not possible.
Chapter 5: Evaluating an RTLS Solution: Which RTLS System is right for you?
When beginning your own RTLS initiative, there’s plenty to learn and consider. First and foremost, what problem are you trying to solve, and what technology configuration will work best for that problem?
Key factors to assess may include:
- What is the environment in which you need RTLS to operate? Are you operating in a heavy metallic setting, office buildings, outside or underground?
- What are your security needs?
- How flexible does your system need to be? Will you need to move manufacturing processes or machinery around in the future?
- What are the sizes, shapes, and materials of the things you want to locate?
- What is the scale of the project you’re pursuing? Are you tracking a few hundred items or thousands, and how large is the tracking arena?
- How precise are your tracking needs? Do you need to locate items by inches, or would a few yards suffice?
- How often do you need updates on the items you locate and track, every few seconds, few minutes or once a day?
- What platform do you use for your data and how do you access it?
Your own in-house facilities management will find some of these questions easy to answer, others may benefit from consultation with an RTLS expert. Others might require field-testing of one sort or another.
When establishing RTLS at a plant it’s important for the manufacturer to determine how that location data will feed into their decision-making processes on the factory floor. If most of the expected benefit is from immediate use, i.e., being able to locate items in the moment, it’s important to know if there will be a visualization system that works for the manufacturer. A simple GUI may be enough. Some users may want a more industry specific GUI. Others may want it to feed directly into their own data or ERP systems via an Application Programming Interface or API. Make sure the RTLS under consideration is compatible with your data system and planned use. Most vendors will be able to make the required adjustments or find an installation or platform partner but talk through those questions before installation.
WISER’s article Everything You Need to Know About Real-Time Location Systems (RTLS) in 2024 describes how RTLS works in more detail.
Just as GPS transformed logistics, manufacturing customers often find additional uses for their RTLS after installation. Once satisfied by the performance realized by RTLS to address a particular pain point, the manufacturer may use it to track critical machinery, assets, inventory, or even introduce safety solutions to protect employees from moving machinery. The nice thing about a modular mesh-network RTLS like WISER is once you have the network installed early it’s easily expandable to solve other tracking needs simply by adding more tags. That’s why a new data stream like location is so valuable for the factory undergoing a digital transformation. It offers immediate benefits in its value proposition around efficiency, optimization, and the bottom line.
What is your Operating Environment? RTLS in Heavy Metal, Reflective Environments
The manufacturing space is a unique environment for an RTLS wireless radio-based system because attaining high accuracy and adaptability can be challenging. A manufacturing facility that has metal and reflective surfaces needs to make sure the RTLS system they’re evaluating is accurate, secure, flexible, and works in this type of environment, as well as working both indoors and out (if needed) and scaling to the required number of assets. Many systems cannot do all of these functions accurately and reliably in these types of environments.
Generally, RTLS solutions use Radio Frequency (RF) technology. These may include Wi-Fi, Bluetooth, UWB (Ultra-Wide Band), and Active RFID (not to be confused with Passive RFID, which unlike Active RFID does not have an internal power source and are instead powered by an RFID scanner). There is some usage of ultrasonic, infrared, and internal motion sensors but those are less common and often used in conjunction with RF-based technologies.
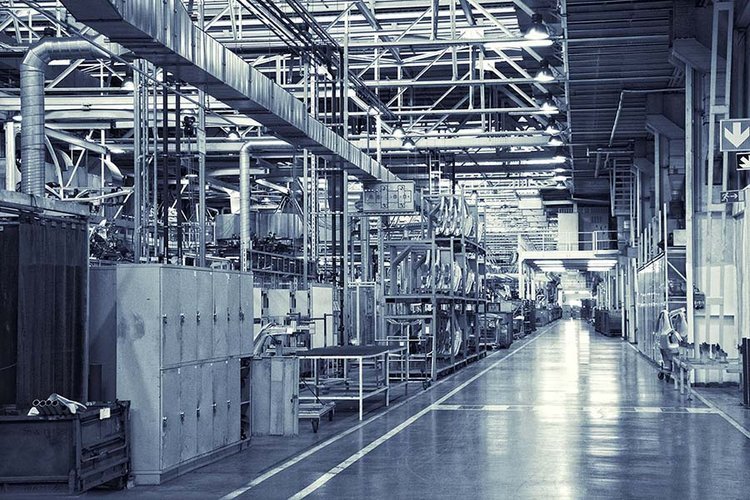
Comparing RF technologies performance in heavy metal/reflective environments
Manufacturing facilities offer a unique challenge for RF technologies. By their nature, factories are busy, noisy places with a large amount of metal and a lot of moving parts. Metal reflects RF and most other surfaces attenuate or weaken any signal passing through.
All RF technologies send out a signal from an object, such as a tag, and an antenna determines the distance from the signaling device. In a metal, reflective environment each signal from a tag will generate the true direct path and many longer reflected paths. To determine location and distance accurately, the goal is to find the shortest direct path between the signaling tag and the receiving antenna. Narrow-band RF technologies, like Wi-Fi, Bluetooth, and Active RFID find the direct path based on signal strength via Received Signal Strength Indicator (RSSI) technology. With RSSI, the system chooses the strongest signal as the true distance, but that leads to inaccurate results in a reflective environment. For example, if there are a pile of boxes directly between the tag and the antenna, the signal will be weaker if it passes through that wall of boxes. The RSSI system will choose the stronger reflected signal which is the false indirect path giving an inaccurate location reading. For this reason, these systems often require direct line-of-sight between tag and antenna.
According to Dr. Seth Hollar, CTO at WISER Systems, “RSSI technology simply cannot achieve high accuracy in a reflective environment. You can set up a mesh of receivers to measure signal strength in a factory setting but there will be too many reflections for it to be accurate. For RSSI to work properly, it would need to be set up outside with no obstacles to get true accuracy.”
In crowded, complex, and reflective environments, such as a factory floor, UWB is the best technology for RTLS.
UWB is a broadband technology that transmits short bursts of broad waves, and the antenna chooses the signal with the shortest arrival time to reach the antenna. Signal strength is not evaluated, only the time to travel. If the signal is weakened by passing through a pile of boxes or even a wall it won’t matter. Software algorithms that evaluate each signal, including which has the fastest time of arrival to the antenna, allow the UWB system to determine which signal is the true direct path and generate an accurate location reading. This enables UWB to perform well in a reflective environment with many obstacles even without line-of-sight.
This aspect of UWB also allows the technology to perform well in high-ceilinged industrial environments. Bluetooth and Active RFID often have a reading limit of about 20 feet because the signal strength becomes too weak beyond that range to capture accurate readings. If a building has a 20-foot or higher ceiling, the system will only be able to track objects directly below, which often requires the antennas to be hung just above the tracking area. Because UWB algorithms rely on alternate measures other than signal strength to obtain accurate distance readings from much longer distances, for example, 100 to 200 feet away. This allows accurate reads and easier implementation in high-ceilinged environments.
UWB technologies also have the benefit of not interfering with common communication protocols such as Wi-Fi or Bluetooth.
What are your Security Needs?
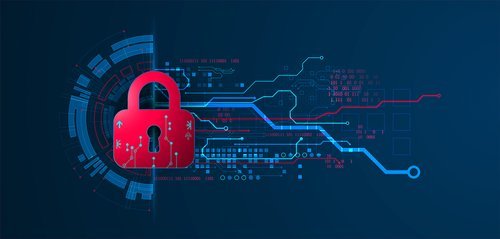
Businesses are using more technology and connected systems to improve processes putting them at greater risk of cyberattacks. This risk has only grown with political instabilities throughout the world, most recently the war in Ukraine.
As manufacturers add more technology to their factories an unfortunate side-effect is an increasing risk of cyberattacks or ransomware attacks. According to the Cybersecurity and Infrastructure Security Agency (CISA), “The Critical Manufacturing Sector is at risk from increased cyber-attack surface areas and limited cybersecurity workforces related to the COVID-19 pandemic.” More recently, CISA published an alert to U.S. companies warning business to be prepared for an increase in “malicious cyber activity” from Russia due to the Ukraine war.
When choosing an RTLS system, it is crucial to consider how to protect the generated data and all the systems using it. Companies that offer on-prem solutions or allow the manufacturer complete ownership and control over the data gives the manufacturer the peace of mind that their location data has the same level of security as other company data inside company firewalls. Solutions that have strong encryption protocols help prevent hacking and data theft. Solutions that limit the type of data shared wirelessly such as only coordinate data, rather than critical data, can help limit the damage of data-theft.
How Flexible does your system need to be?
A major goal of Industry 4.0 and the smart factory is analytics to quickly translate data into intelligence that improve productivity and cuts costs. In the SAE International’s Smart Manufacturing Report (August 2020), Erik Jofesson, Head of Advanced Industries at Ericsson is quoted as saying, “Especially with faster product cycles and increased customization, the manufacturing setup must be as flexible as possible to be competitive.” For process changes, that can mean moving inventory to other areas, moving stations, or swapping out machines that can alter where the location system needs to focus and even the layout of the factory. Relocating the RTLS solution every time a station is moved, or a floorplan rearranged can be an expensive and major undertaking, if the system is not flexible.
Companies can assess the flexibility of a proposed RTLS solution based on the calibration needs at initial install. If the location system requires extensive calibration steps that cannot be done remotely or by the manufacturer’s own staff, that is a sign that the system will require the same level of recalibration any time there are significant changes to the shop floor. All Wi-Fi and Bluetooth solutions and many UWB solutions do require extensive manual calibration with the movement of any antenna. Not all do. For example, WISER systems UWB solutions do not require extensive calibration at install and for single antenna movement no re-calibration is required. If recalibration is required, it can be accomplished by the system itself by the push of a button. If flexibility is important in your solution, make sure to assess calibration requirements.
Additionally, for a company expecting to roll out an RTLS solution over many sites, the ease of installation can be a crucial factor in the purchasing decision. A company that can easily train its own staff to install and calibrate a system can significantly decrease the cost of a wide-scale installation and should be considered when choosing between RTLS solutions.
Another consideration can include whether line-of-sight is needed when positioning antennas. As mentioned in the section on Reflective Environments, UWB is the only technology that can accurately determine location without line-of-sight. When evaluating any solution, it may be important to determine whether the antenna is able to monitor an area if a machine blocks its line of sight to the monitored area. If it cannot, and line-of-sight is required, additional antennas must be installed and calibrated after a change. In addition, any general management throughout the factory, such as the use of cranes could temporarily block an antenna’s line of site suggesting no line-of-sight systems may still be required even in areas where line-of-site seems assured.
If there is a need for a dense array of antennas this would indicate the system has difficulty collecting an accurate signal. Again, UWB generally requires fewer antennas than any other RTLS solution. For non-UWB solutions, it is likely that any significant changes or increase in trackable items will reduce the system’s functionality and more antennas or repositioning will be required to achieve the earlier level of accuracy. These are good questions to ask before purchasing a system. No factory wants to invest in a cutting-edge tracking system that can’t adapt to the changing needs of a facility over time.
Chapter 6: WISER Systems: A great solution to the manufacturer’s RTLS challenges
WISER Systems has been developing its cutting edge UWB-based RTLS solution for years. The result is WISER’s own Redundant Radio Location and Tracking (RRLT), which has optimized accuracy and flexibility that meets the needs of the modern manufacturer. The high-density WISER ATLAS™ RTLS and lower tag density WISER Locator™ solution both perform well in highly reflective environments and are easy to install and calibrate. This means that out of the box, WISER customers can see immediate benefits from the system by seeing where assets are at any given moments and if they choose to adjust their processes or work plan, the WISER system maintains the same level of accuracy. To learn more about the WISER RRLT please visit our product descriptions at WISER ATLAS and WISER Locator.
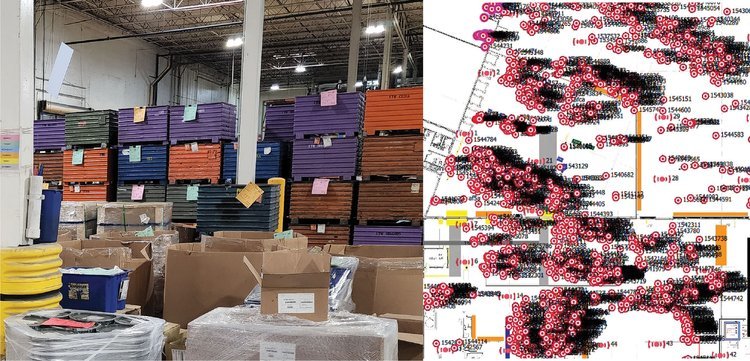
SWD, a metal finishing company recently installed WISER’s ATLAS system to track thousands of work orders as they moved through various finishing steps. WISER’s system gave SWD visibility into where these work orders were at any given moment. Workers no longer needed to search for missing parts of orders or misplaced boxes. They could immediately look up any individual work order on the WISER ATLAS app on their phone, tablet or other device. According to SWD CEO Matt Delawder, “On any given day we needed the ability to track up to 4,000 parts, with the capability to reassign 500 work orders to tags each day. This is the best productivity improvement we’ve done in years. It will change our entire manufacturing process.”
SWD is an active facility tracking metal product in metal bins that are stacked on top of each other or moving around. Only WISER’s RRLT solution could manage the reflectivity challenges and need to adapt to process variation this customer required.
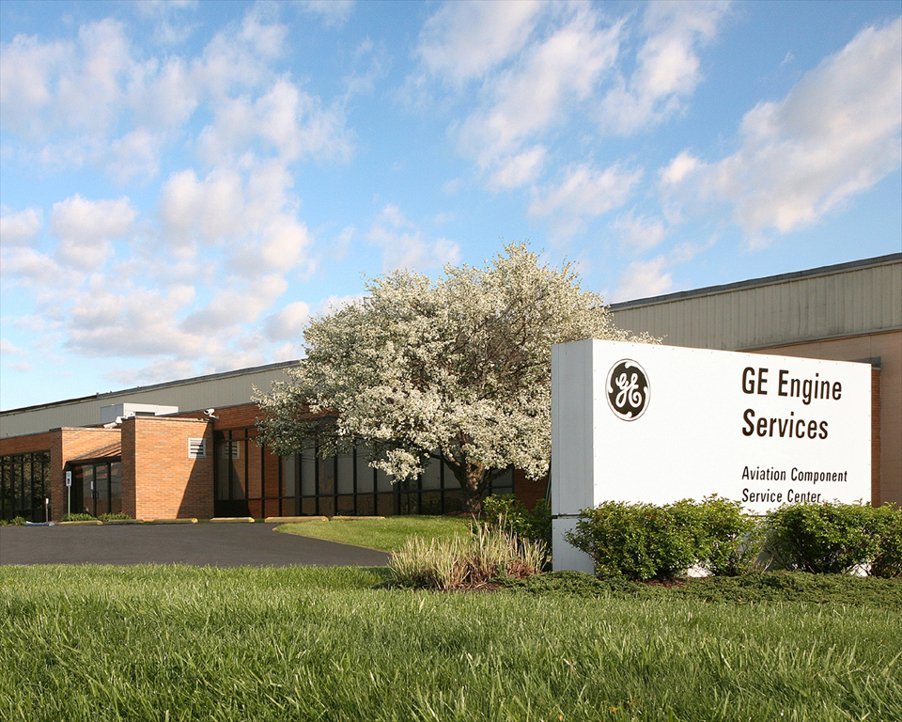
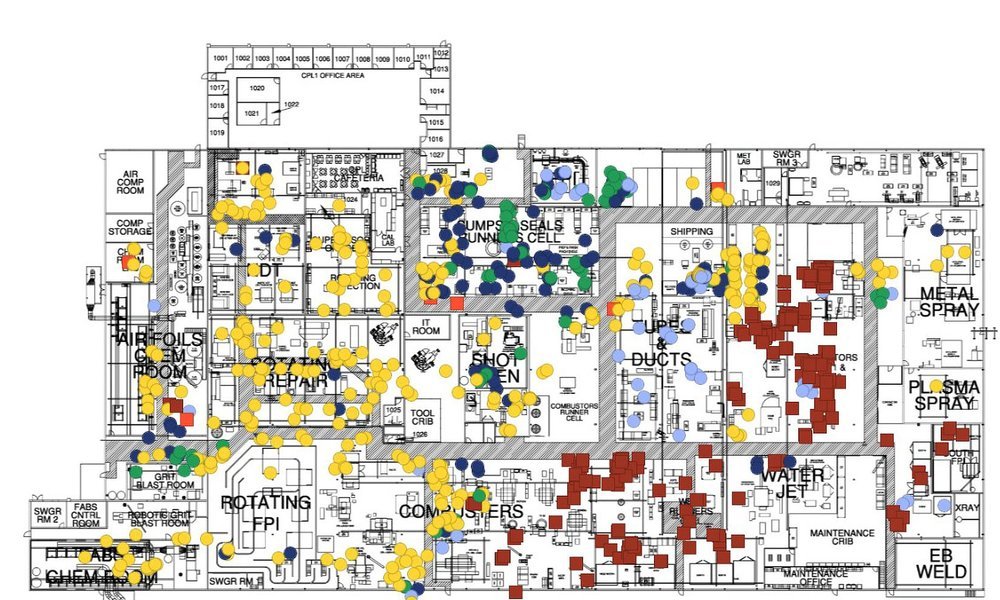
GE Aviation’s Cincinnati-based ACSC Maintenance, Repair and Overhaul (MRO) facility provides another example, according to Kyle Mosier, Site Digital Leader, “better work-in-progress (WIP) management was a major need at the plant. Part tracking and flow management were huge issues at our plant—we had this as a top priority for a few years. Prior to installing an RTLS automation, company staff relied upon knowing the location of each part’s last known work operation when they tried to find parts. Now,” he said, “we have an accurate snapshot of our shop that we can trust and rely on. After installing the new WISER ATLAS, productivity in the production control area increased by over an order of magnitude (12 times),” according to Mosier. “Being able to achieve process capacity improvements quickly is a key advantage of a high quality RTLS system that will translate into increased profitability,” he added. Read the full article in MRO Management, pages 10-11.
In both facilities, the highly reflective environment, high ceilings, and active movement between stations made Wi-Fi and Bluetooth solutions much less reliable. The unusual flexibility of the WISER solution allows SWD and GE facility to make changes to their factory processes without degrading RTLS accuracy in any way.
Both customers also investigated the security provided by alternative RTLS solutions WISER Systems has made security a priority. WISER’s UWB RTLS solutions ensure customers own their data, and many customers keep this data in on-prem servers. The data is encrypted, and it lacks identifiable features of item name or type, for added security. For more information about how WISER’s system protects your data.
WISER RRLT does not employ cameras, biometrics, facial recognition or personal cell phone tracking—things employees often consider intrusive. The system utilizes a segregated, on-site network of very low-power ultra-wideband (UWB) devices that can be focused to track only within designated workspaces.
The WISER Locator generates and distributes data using a segregated network of ultra-wideband (UWB) devices. Isolating location data in this way protects data from being scraped over a network. WISER hardware can also be isolated from sensitive company intranets. Furthermore, the WISER Locator does not require WiFi or other pre-existing wireless networks to operate. Not requiring company WiFi or cloud services to operate also helps keep this valuable personal data safe from hackers or other malicious actors. WISER solutions can operate in a secure cloud configuration or entirely on-premises, which adds another layer of control and security for end users.
As a distributed, localized, edge solution, WISER devices can be non-individualized to provide meta-data only. Or they can be individualized only if there is a need for a pre-specified event such as safety or perimeter violations. Devices are never tracked outside the pre-determined workspace footprint.