What is RTLS?
The term RTLS typically refers to localized positioning systems, as opposed to global positioning systems such as GPS. While time and location are the obvious common aspects of both, identification is an additional important feature of RTLS, even in cases where identifying information is safeguarded.
In essence, RTLS shows the what, where, and when within a defined locale, quantifying these factors in a way decision-makers can understand. For instance, RTLS could be used to show which forklift (what) crossed a given picking lane in a warehouse (where) at a specific time (when). Another example: RTLS can visualize which shippable container (what) was loaded onto a specific truck (where) at a given point during the workday (when).
Because RTLS describes a wide array of location intelligence solutions, it’s helpful to disambiguate. For instance, the term RTLS generally encapsulates systems providing proximity-based data or actual coordinates. It’s also sometimes used for systems that identify devices at set choke points, providing temporary location at a point of scan. Since point-of-scan systems don’t show continual / real-time location, this guide won’t explore these systems in depth. Rather, the focus of the following sections will be systems that continuously provide identification, location, and timing data, the what, where, and when mentioned above, even while assets are on the move.
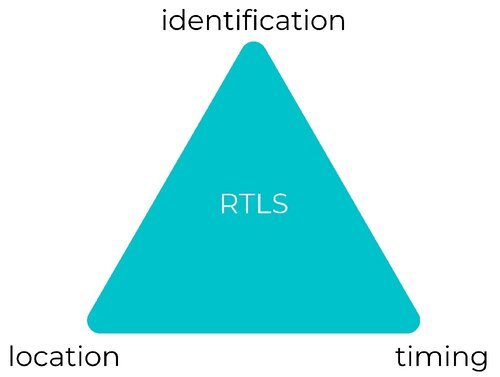
RTLS is a critical component of the Smart Factory, Digital Transformation, and Industry 4.0 family of advanced digital technologies. For many operations, a location intelligence solution such as RTLS may be the first technology they try.
According to Deloitte’s article, 2024 Manufacturing Industry Outlook, “Manufacturers should continue embracing digital transformation to contribute to a competitive and resilient future and to help tackle ongoing manufacturing challenges.”
RTLS has been around for more than 20 years, and most technologies powering RTLS are now well known, and in production. What’s less understood is the difference between these technologies and how to evaluate the costs and benefits of each in order to select the best solution for your industry/facilities’ tracking needs.
RTLS technologies may be customized to the environmental peculiarities of each site, the volume, types, and value of assets that need to be tracked, and the tracking frequency and accuracy required – from room-level to within inches.
The real-time Location Systems Market (RTLS) will be worth $12.7 billion by 2026, according to the new research report, published by Markets and Markets™.
The Difference Between RFID and RTLS, and the Technologies Used in RTLS
RFID technology uses radio waves to identify and track tags attached to objects, offering point-in-time data when a tag is within range of a reader. While RFID is effective for asset identification and data capture, it has limitations in precision and range. RFID systems require a clear line of sight for accurate tracking, which means they can only locate assets that are close to the reader. Passive RFID tags, which lack a battery, are cost-effective but not ideal for asset tracking due to their limited functionality. On the other hand, active RFID tags can transmit data when near a reader but tend to be more expensive due to the need for purchasing readers.
Real-Time Location Systems (RTLS) utilize technologies like Wi-Fi, Ultra-Wideband (UWB), and Bluetooth Low Energy (BLE) to provide continuous real-time tracking of assets and people within a defined area. RTLS offers superior coverage and accuracy compared to RFID, delivering uninterrupted real-time data across a space. This makes RTLS particularly valuable for industries with time-sensitive and cost-intensive operations, such as production, logistics, and healthcare. For instance, companies can use RTLS to enhance worker safety by monitoring employee locations in real-time.
There are more and more innovative ways to make real-time location a reality. By far the most common approach is using radio frequency identification (RFID) technologies, like WiFi or UWB, however, WISER’s RFID system uses a patented Redundant Radio Localization and Tracking (RRLT) UWB-driven technology, making for a more precise RFID.
In general, an RF approach remains the same across technologies. Wireless transceivers—often called tracker tags or simply tags—mark the objects or personnel being located and tracked. Meanwhile, a system of reference points in known locations reads transmissions from these tags to calculate actual timing and location data. These reference points can be called antennas, anchors, or sometimes beacons depending on the system being used.
Some systems calculate location data at the edge, and some send it back to a local or cloud-based server first. Likewise, one system can use triangulation while another uses trilateration, some require a clear line-of-sight between RF devices though others function without it, and parameters for hardware installation span the gamut.
What’s the Difference Between Asset Tracking and RTLS?
The terms RTLS and asset tracking sometimes appear side by side, even being used interchangeably. Asset tracking can refer to many tools well outside RTLS. The common ground lies in both identification, and tracking. The key point of difference lies in what ‘tracking’ means in the first place.
Asset tracking can describe anything from a spreadsheet to a library catalog to a true location intelligence system like RTLS. Many asset tracking solutions are software tools designed to intermittently log data entered manually, not to autonomously track while providing continuous live updates. As such, asset tracking often entails systems to account for things at the momentary point of data log, whether that’s the moment of a scan, the time when inventories are updated, or another metric. Continuous autonomously-derived location data is not always part of the picture.
Barcodes are a prime example of a basic asset tracking solution. Barcodes provide identification but are not equipped with continuous location or timing data. Even when scanned frequently at specific, set locations, the timing and location data is temporary rather than current. On the other hand, there are numerous ways to use RTLS that wouldn’t be described as asset tracking at all. For instance, non-optical navigation systems or location-based worker safety applications use RTLS outside the scope of what is typically referred to as asset tracking.
Sometimes identification at point-of-scan is the only information needed; scanning a library book or a train pass are examples. In other instances, precise and continuous location data is a real game changer, whether due to frequency of asset movement, where asset loss is particularly dangerous or expensive, or because location data enhances key metrics for efficiency.
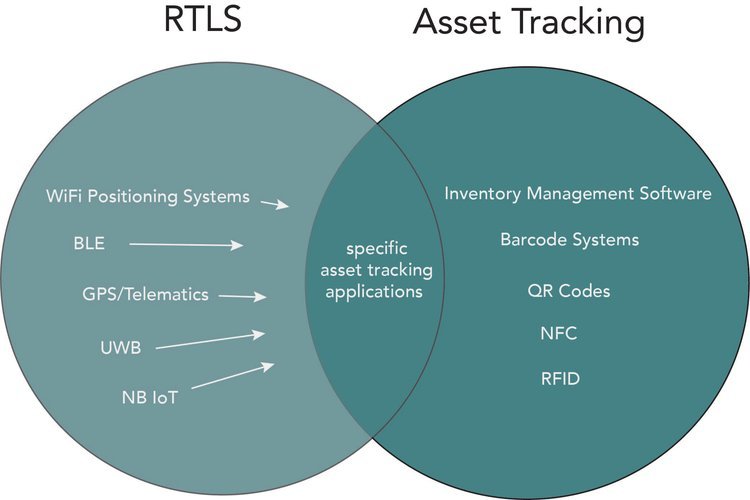