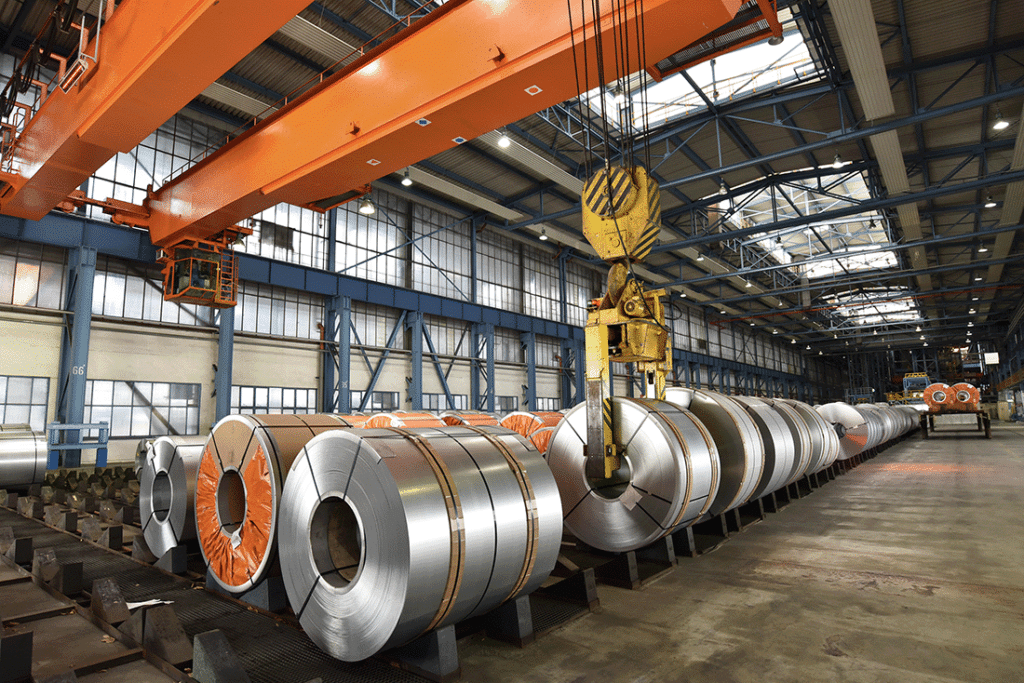
You can add asset tracking to the growing list of tech terms connected to Industry 4.0. Asset tracking has been a key process improvement practice since before the invention of the barcode. It should be no surprise that practices for managing inventory, finding movable items, and tracking the status and locations of key assets will continue to fuel innovation and cost-savings across industries.
What is asset tracking?
The term asset tracking typically describes systems for managing inventories of things like storage containers, pallets, individual tools, electronics, or even vehicles.
Some solution providers make a distinction between asset tracking and more specific applications, like forklift tracking or yard management, but the principle is the same in each case: Asset tracking is a systematic approach for keeping tabs on items that are useful, valuable, or simply losable.
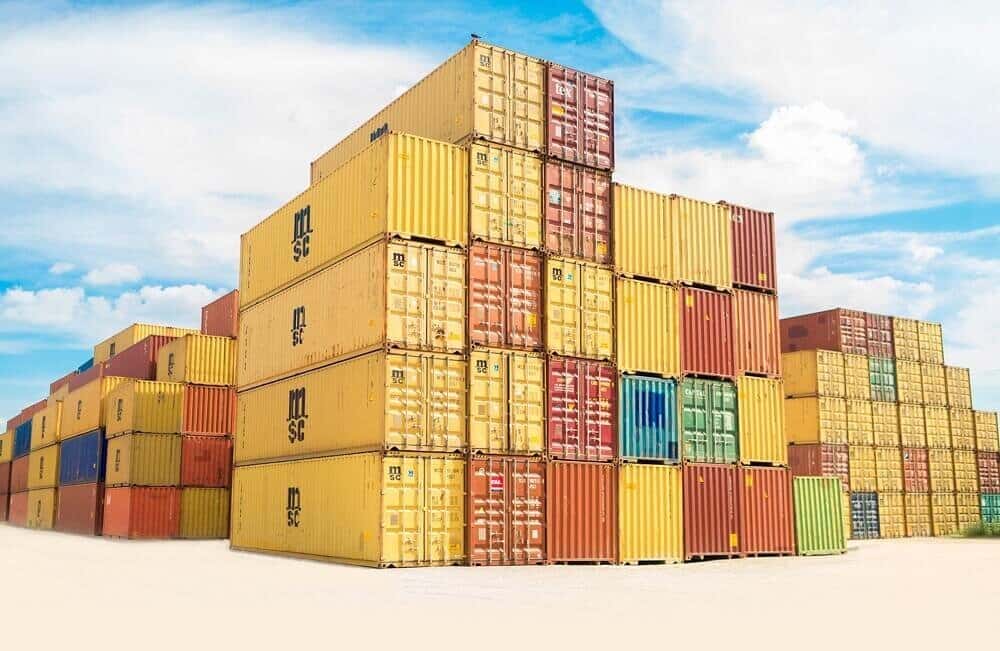
Some asset tracking solutions focus purely on the software side, facilitating inventory checkout, check-in, and general management. This article will focus on systems to actually locate or track physical assets, be it in real time or not.
A number of different technologies feed into this concept. For instance, asset tracking could refer to automatic identification systems like barcodes. It could describe systems that report asset status only at specified times and places, as is the case with RFID readers installed in doorways or hand-readers sent out to manually scan inventory at routine intervals. Asset tracking can also be done with real-time location systems (RTLS)—systems that autonomously register as things move or are moved.
No matter which technology you use, asset tracking still won’t solve every problem. Even the best implementation with the best asset tracking system leaves room for mistakes or miscalculation. The following are a few main points to keep in mind—things asset tracking typically won’t do for you:
- Remove all manual labor or work processes
- Rewrite all your operational routines
- Eliminate human error
- Invalidate everyone’s job
1. Asset tracking won’t remove all manual labor or work processes
In-the-moment accountability for your assets can save a lot of effort, but it won’t ensure that every asset stays where it belongs. You’ll probably still have to go out and grab a tool or a container from somewhere else. Your work teams will still need to restock shelves, shift stacks of pallets, or put shippables into outbound vehicles. With legacy asset tracking technologies like RFID or barcodes, you might even need to update a digital inventory or send a scanner out to find certain items.
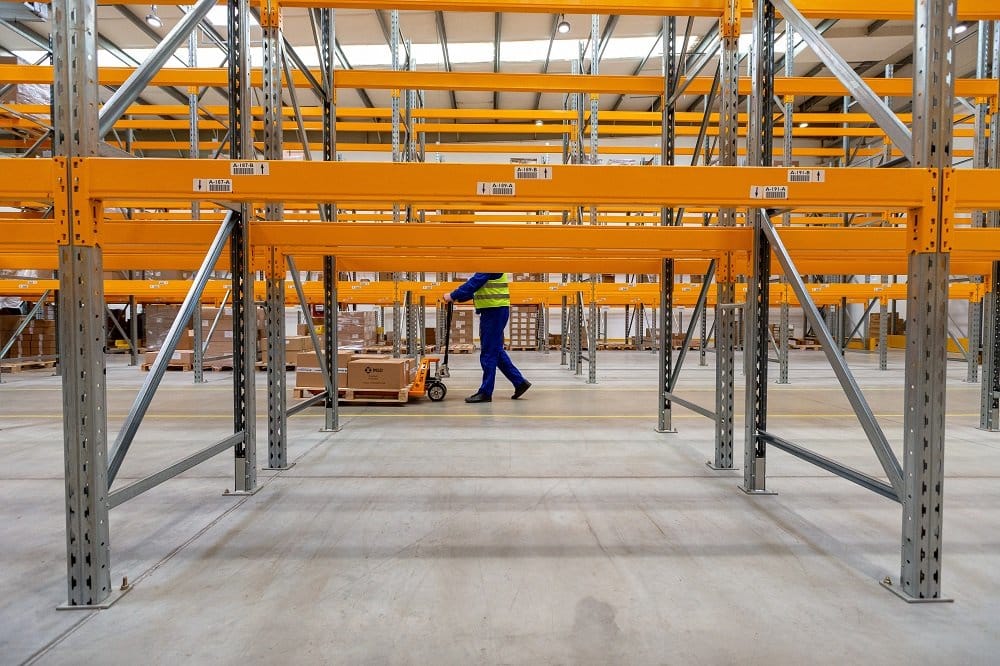
Newer, active systems for asset tracking, like RTLS via ultra-wideband (UWB) or Bluetooth Low Energy (BLE), can reduce an end-user’s physical efforts. One way they do this is by autonomously updating logs or inventories as items move. However, this still requires the effort to retrieve misplaced items or to keep things where they belong in the first place.
2. Asset tracking won’t rewrite all your operational routines
There’s no need for new asset tracking procedures to disrupt every process already in place. Granted, a clunky or half-baked asset tracking system could cause new work or slow down some existing processes. Also, implementing new technologies like asset tracking will always require some training time before it can be utilized to its full effect. In the end, however, asset tracking solutions are designed to solve more problems than they potentially create.
As with other technologies, adopting asset tracking might introduce friction in some work habits or written (and unwritten) procedures in your organization. A careful assessment of where such a system fits with work routines should thus be part of assessing the system itself. The key to asset tracking is that it allows more options rather than fewer to solve problems, improve uptime, and cut unnecessary expenses.
New systems of asset tracking don’t usually need to replace investments in older systems either. Here’s an example: WISER Systems, which specializes in the RTLS side of asset tracking, worked with a manufacturer who already used both an older RTLS data integration and a barcoding system for products being manufactured. To avoid replacing what already worked, WISER supplied new hardware—as a drop-in replacement for a legacy RTLS—while preserving both the data integration and the barcoding system the manufacturer already relied on.
This solution enhanced the utility of the existing technology rather than undermining or replacing it. Finding complementary solutions like this might take some back-and-forth, but the end results help minimize new costs and ameliorate the learning curve of adopting a new system.
3. Asset tracking won’t eliminate human error
A worker’s mistakes can be wildly lucky on occasion, but they’re more likely to be disastrously expensive. No asset tracking system will stamp out this risk, since error will always be present where humans work.
A key boon for asset tracking is the ability to make errors visible more quickly—perhaps even before they cause any real damage, danger, or expense. For instance, by tracking pallets moved to the incorrect loading dock, site managers can know before an item is shipped in the wrong direction. Similarly, real-time visibility of a machine needed on a production line enables workers to get that machine in place in advance, preventing unplanned downtime. Or, by tracking perishable goods, workers can know well in advance that the asset needs to be moved, refrigerated, etc. to avoid expiration.
Instead of waiting to learn about errors once they’re beyond repair, asset tracking solutions enable you to detect location-based problems the moment they begin. You’ll need to keep training and disciplining your workforce as always, but you can also give workers more leeway if you know the what, when, and where of key problems.
4. Asset tracking won’t invalidate everyone’s job
It’s not uncommon for everyone to do their share of asset-hunting. Whether at home or at work, most of us lose things on occasion and spend unplanned time searching for those lost items.
Searching for missing assets is especially common in settings like warehouses, factories, and hospitals, where the risks of lost or damaged goods are high. Furthermore, because nearly everyone shares in the load of looking for lost things, asset tracking systems are often relevant for workers in quite a few different positions.
Think about technicians needing specific pieces of machinery, quality-assurance or shipping personnel who’re looking for a specific order, or forklift operators who need both the right pallet and the right forklift. Because each of these workers have other responsibilities above the work of finding the right thing, asset tracking processes don’t change their work much beyond speeding up the search-and-find protocol. The only jobs that asset tracking can truly eliminate are positions focused exclusively on finding things or taking inventory.
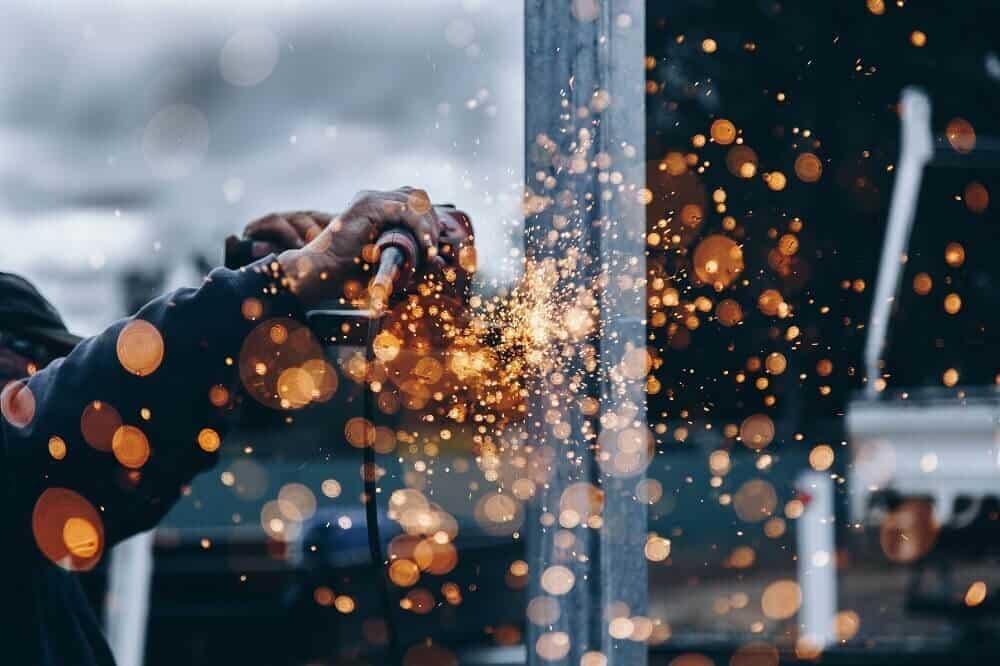
It’s more and more possible for robust asset tracking to cut the need for an inventory check of any sort. It’s also possible for asset tracking systems to make other manual record-keeping processes obsolete, further simplifying workflows. Per previous sections, one possible change for inventory personnel, as asset tracking becomes more ubiquitous, is a shift to focusing on organizing and moving assets where they belong, rather than simply finding and accounting for them. While this work can also be automated in some environments, human labor is still a key component in most settings with designated storage areas or many moving parts.
What this really means is that asset tracking enables workers to spend more time anticipating or preventing problems and less time merely responding to them. Heavy machinery operators can stick to operating the machinery instead of spending time searching for it. Likewise, technicians can spend their time on tasks requiring their specific expertise. Rather than purchasing extra inventory, rummaging for lost items, or otherwise doing damage control, these workers can focus on being truly productive.
Bonus: A few things asset tracking WILL do
There’s plenty to be gained with a solid asset tracking system.
Nearly any solution for asset tracking will equip you with a more systematic approach to managing inventory. For example, purchasing and holding excess inventory is a big expense by itself. There’s also the opposite problem—not having enough deliverables when you need them—which can be staggeringly expensive due to lost business opportunities, delayed orders, fees to expedite shipments, and eroded trust with clients. Asset tracking takes a big step toward solving these issues, giving you the data to forecast when you do or don’t need to replace materials and replenish your stockpiles.
If you utilize RTLS for asset tracking, you get the added benefits of motion histories, actual task completion timelines, and other quantified metrics about how location-based work is happening. RTLS generates the requisite timing and positioning data to find bottlenecks and identify how long each stage of production, picking, packing, or shipping actually takes.
Effective asset tracking can also autonomously identify safety or compliance hazards. Risks of perimeter breach, asset expiration, or the proximity of dangerous items can all be reported and visualized in real time with the right tools in place.
Ultimately, asset tracking saves you the headache of hunting for things you need or watching for errors that could be detected with effortlessly with the right data.
In Closing
The need for better supply chains, more optimized material handling, improved asset utilization, and maximized inventories only continues to grow. The good news is that there are more and more asset tracking options available to keep pace with these processes today.
Asset tracking isn’t a miracle cure for every operational problem, but it is a game-changer that’s here to stay.