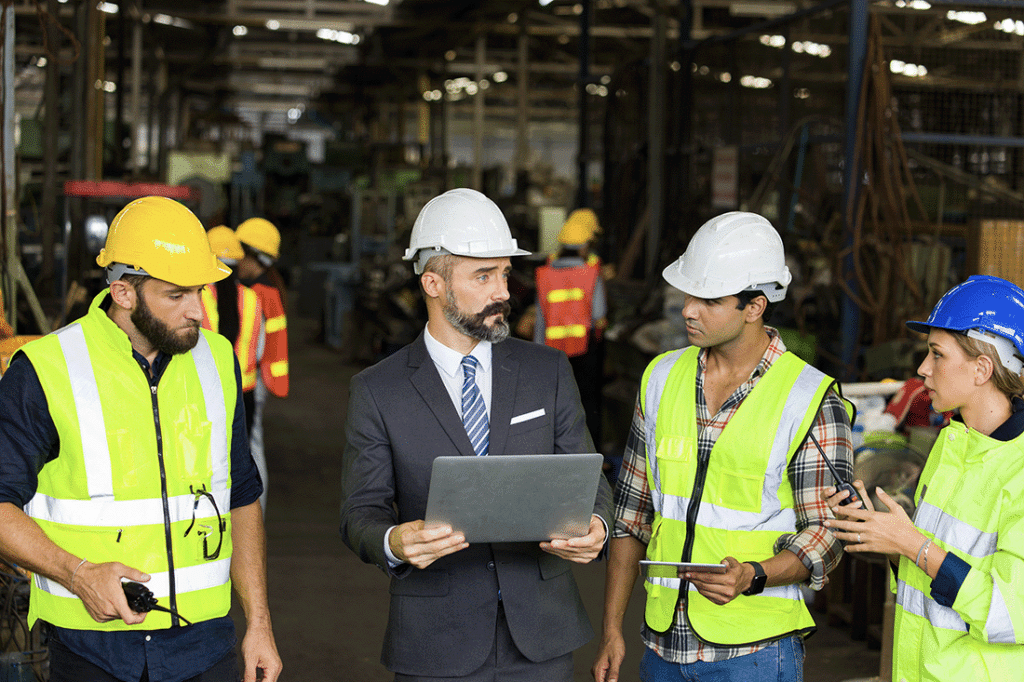
Nearly every worker is responsible for some physical asset related to their job. Depending on your industry, this could range from a uniform, badge, computer, work phone, or valuable machinery, parts, or inventory used in the manufacturing process.
We all know the stress of misplacing an item entrusted to us. While losing a single item might seem minor, when hundreds or thousands of workers lose things over time, the costs and inconvenience can add up significantly. It’s no wonder that more companies are turning to asset tracking systems to reduce the risks of lost or misplaced items. These systems encompass inventory tracking and management software, checkout protocols, barcodes, real-time location systems (RTLS), and custom solutions that combine various technologies.
Most asset tracking initiatives aim to improve the bottom line by saving money or generating revenue. The financial implications are vast, but here are seven common areas highlighting both the problem and the solution:
· The dollar value of lost inventory
· Expenses for replacing missing items
· Work hours spent checking inventory or searching for missing items
· Unplanned delays to work routines
· The value of unused or unneeded physical space
· Costs to implement asset tracking or inventory management systems
· Revenues generated by improving your process
· Investing in effective asset tracking can address these issues, ultimately leading to significant cost savings and improved operational efficiency.
1. The Dollar Value of Lost Inventory
Calculating the dollar value of lost inventory is often straightforward—if you can first identify which items are missing.
Start by evaluating the current dollar value of your inventory to grasp the importance of effective inventory management. Next, assess the accuracy of your inventory records. Consider shipping schedules, replenishment, and replacement timelines for outdated items. This will highlight the potential savings from improved inventory tracking.
Inventory can go missing in numerous ways: workers might ship the wrong item by mistake, leave an asset somewhere and forget about it, or miss scans when removing items from inventory. These issues accumulate over time, leading to inaccurate records.
Regardless of your industry, maintaining an accurate and up-to-date inventory picture is crucial. Effective inventory management can prevent financial losses and enhance operational efficiency.
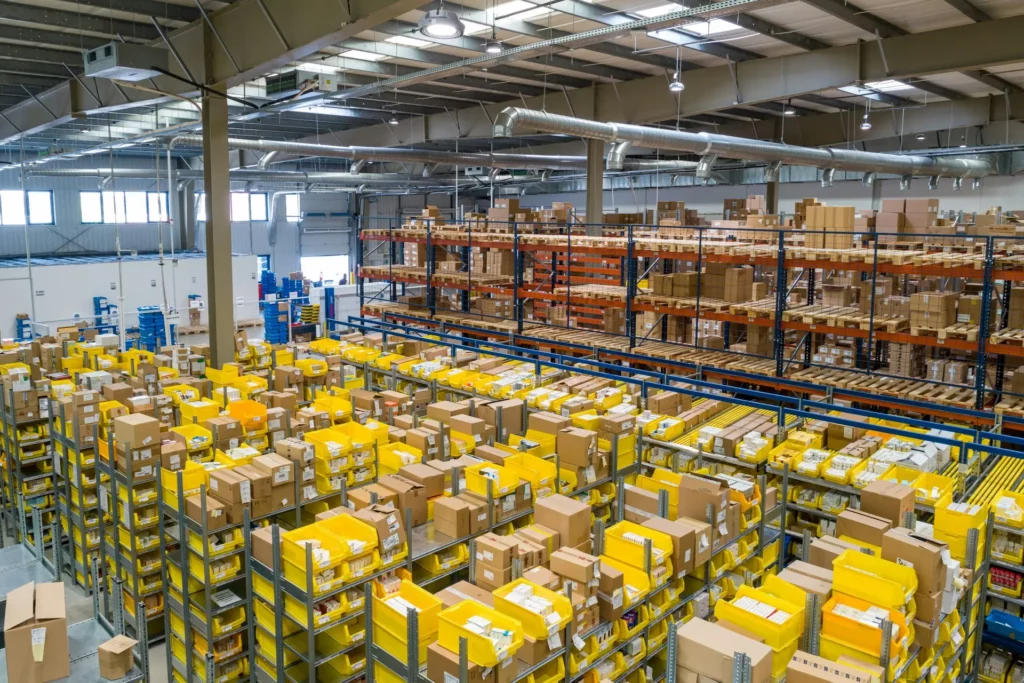
2. Expense of Replacing Missing Items
Replacing missing assets involves much more than just covering the cost of the lost item. In some cases, missing assets might have been stolen. For example, one WISER customer discovered their missing equipment was being sold on eBay, significantly impacting their profit margins.
Delays due to waiting for new products to be manufactured or shipped can be costly. Additionally, replacing lost assets often requires purchase order requisitions, approvals, third-party buyers, and other bureaucratic processes, making the replacement far from simple.
3. Work Hours Spent Checking Inventory or Searching for Missing Items
Labor costs are one of the primary reasons to improve asset tracking. Businesses that frequently lose inventory often spend significant time searching for it.
The searching process can be highly inefficient. In many settings, permanent employees with other critical duties end up spending valuable time searching for items. For instance, in hospitals, nurses and doctors often hunt for missing wheelchairs or IV pumps, while in manufacturing facilities with heavy machinery, technicians search for calibrated tools needed for servicing.
According to Kyle Mosier, Site Digital Leader at GE Aviation, ACSC, “One of the biggest challenges in facilities like ours is keeping track of all the moving parts. Prior to installing the WISER System, productivity was lost due to searching for lost or misplaced parts and work orders. Since installing the WISER system productivity has increased by 12 times for production control and we’ve been able to increase our capacity by 15%, and reached ROI in three months.”
4. Unplanned and Harmful Delays to Work Routines
Unplanned downtime extends beyond the hours spent searching for missing items. Time spent looking for lost goods detracts from revenue-generating tasks. Facilities often need to halt production, shipping, and other key services during inventory routines or unexpected delays caused by missing items.
In manufacturing, unplanned downtime can be as expensive as $260K per hour, according to Aberdeen Research. A large automotive company indicated they could lose up to $1M in an hour if a single assembly line halted due to misplaced equipment.
Even something as simple as a misplaced work order can lead to unintended downtime. Regardless of the specific scenario, it’s challenging to pursue revenue-generating activities when operations are stalled.
5. The Value of Unused or Unneeded Physical Space
Owning, renting, or maintaining physical space incurs significant costs. In industries like shipping, warehousing, and storage, unused space can be a huge source of overhead. Maintaining temperature-controlled, insured, secured, and cleaned spaces adds to these costs.
Unused or poorly managed space can also lead to longer search and inventory times, adding further inefficiencies. While consolidating inventory may not lower rent or taxes, having an accurate inventory count can help prevent overpaying for space and reduce maintenance costs.
6. Costs to Implement Asset Tracking or Inventory Management Systems
The costs of owning and operating an asset tracking solution are crucial to consider. These costs range from facility shutdowns for infrastructure changes to software subscriptions and employee training hours.
Implementing an asset tracking system typically involves upfront installation and onboarding costs, along with ongoing maintenance and upgrade fees. Licensing arrangements may also apply, depending on the number of assets tracked or the tier of services accessed, in some cases.
By understanding the expenses outlined above, businesses can accurately assess the ROI of asset tracking and determine if it’s a worthwhile investment. For companies managing high-value items or facing significant losses from missing inventory, asset tracking can be crucial.
For example, one company approached us after losing $1.2 million worth of copper overnight. This substantial loss highlighted the importance of a robust asset tracking system to prevent similar incidents in the future.
7. Revenues Produced by Improving Your Process
WISER worked with a small company whose sales staff spent 40% of their work hours searching for the correct items to ship. By repurposing even half of these hours for sales activities, the company could potentially increase revenues by 15-20% annually.
This highlights the revenue generation potential of implementing asset tracking solutions. For instance, if a factory that closes one day a month for inventory updates could instead run manufacturing, the increase in sellable goods would be significant. In healthcare, knowing the location of key supplies or equipment can enable more patient visits, enhancing service delivery.
IoT approaches to asset management have generated an average of $9.4M in new revenues per individual initiative, according to one large study. Beyond financial gains, improved asset tracking can also boost stakeholder trust and satisfaction by ensuring timely deliveries and safeguarding entrusted goods.
Original post first appeared in IIoT World, written by Stephen Taylor